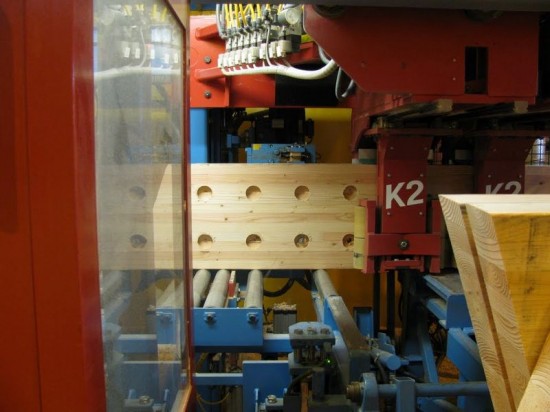
Walking through many a jobsite, I have always felt at home with the smell of wood dust, the whirring noise of circular saws, and welding sparks flashing in the distance. These features are results of materials being cut and/or fabricated on site, and often times lead to unnecessary waste, whether it is due to un-intention or carelessness. So how can we be more efficient about constructing a building? Could maximized prefabrication be the solution?
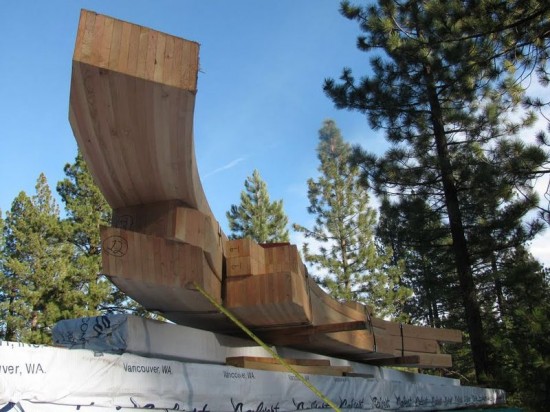
The What: Based in San Francisco, California, IDEAbuilder (Interactive Design, Engineering, and Architecture) is a strong proponent of using technology to design and prefabricate buildings which in turn saves human and material resources and energy during construction.
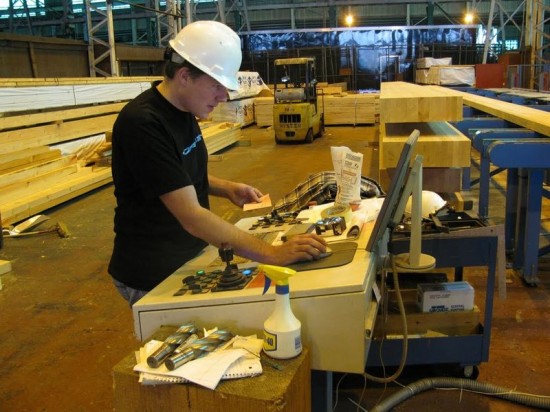
The IDEAbuilder System approach is to work with architects and builders to produce detailed construction drawings that can be readily adapted to a software program for computer-aided robotic manufacturing. The software program first models the project in 3D and enables the team to virtually work out any design and construction issues. Afterwards, a chosen manufacturer uses the computer-aided robotic manufacturing software program to fabricate all the wood and steel pieces required for the building. Each pre-fabricated component is then labeled, packed in assembly kits, and delivered to the jobsite. Example components include roof trusses, wall framing assemblies, and moment frames. With instructions and assembly plans keyed with identification tags in hand, on-site crew members can assemble the prefabricated pieces to close in the building quickly and efficiently.

What is “green” about robotic manufacturing process is that it can cut down the overall construction timeframe of a building and reduce waste. Computer-aided fabrication in the shop reduces potential material waste generated on site, and provides precision cut components fabricated with a speed faster than that of manual fabrication methods. Ready to assemble components would prevent potential time spent on human fabrication errors and problem solving on the jobsite, as well as reduce the need for the one-man-one-power tool use of electricity. The “assembly kits” essentially enable builders to build efficiently within a short timeframe.
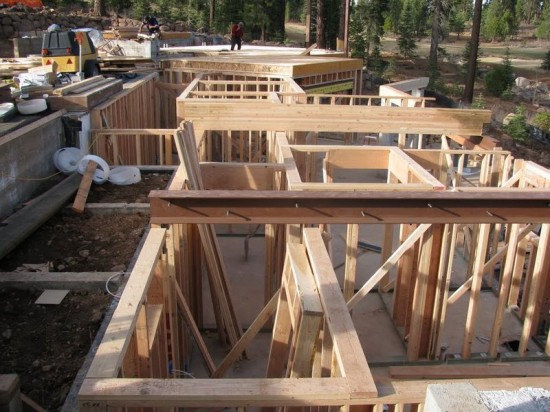
The Who: Greg Howes is the founder of IDEAbuilder. Having spent 10 years running his own residential building company and 10 years in the technology field, he combined his expertise to take on the challenge of making buildings more efficiently with the use of technology. According to Greg Howes, “computer-aided manufacturing of wood homes is tried and proven as it is the standard practice in Switzerland, Germany, and Scandinavia. It is a cost effective, scalable green way to build homes, be resource efficient, and reduce human errors.” In the past few years, Greg and his team have been working with architects, manufacturers, builders, and real estate developers who want to embrace computer-aided manufacturing technologies and build this way.
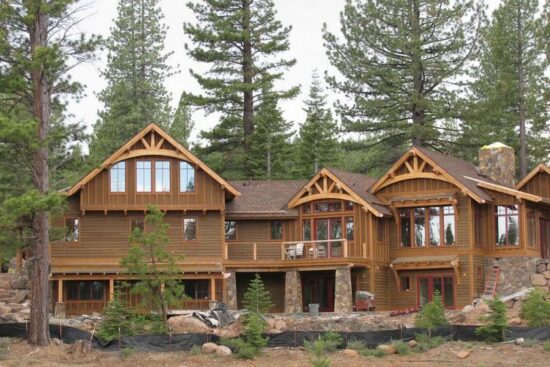
IDEAbuilder’s proof of concept house is currently being completed in Truckee, California. It is a 5,000 square foot house and it took less than 4 weeks to dry in! If conventional on-site fabrication and construction methods were implemented, it could have taken 5 to 6 months to dry in. The contractors were elated that construction went so quickly. The house framing started in November 2008 and the owners are almost ready to move in now! Imagine if we could build all our buildings more efficiently as does the IDEAbuilder System recommends. Think of how much resources and energy we could conserve if we utilized robotic manufacturing. Is this the way to a greener future?
Be the first to comment