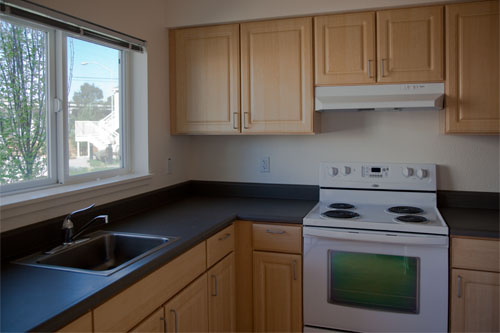
Value engineering. The term often evokes trimming down a project. However, used properly, it can be a positive tool that helps one take a systematic approach to evaluating a building system or product from different perspectives. In the realm of greening a project, value engineering is an important part of the decision making process.
Value engineering was developed during World War II at General Electric, when a shortage of material, components, and labor affected the GE production lines. Their attempts to address these issues occasionally led to improvements in the product and reduced costs. Born was the concept of value engineering—a “function-oriented, systematic team approach used to analyze and improve the value in a product, facility design, system or service; a methodology for solving problems and/or reducing costs while improving performance and quality requirements.”
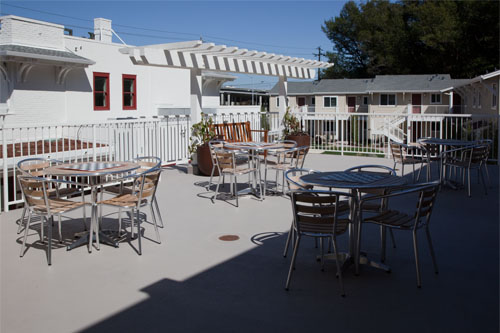
In developing The Fireside, Citizens Housing Corporation (CHC) integrated value engineering into the design process to achieve its green building performance goals and stay within budget. Being conscientious of how different products would impact the environment as well as affect upfront and long term building costs, team members were able to make smart choices in environmentally responsible products.
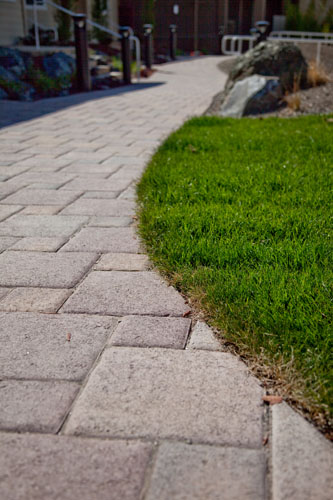
The development team worked closely with the architects and contractors to establish a design baseline beyond CHC’s green design and construction standards. The architects generated a list of green alternatives for products ranging from framing wood to floor coverings, and the contractor priced them and/or proposed new alternatives.
For the purposes of evaluation, there were 3 categories of green products:
- Basic “must do” items, also known as the “low-hanging fruit,” such as displacing Portland cement with fly-ash in concrete, using no-VOC paints, and selecting flooring made with recycled and/ or renewable materials were essentially no-brainers.
- Systematic assemblies such as using FSC certified framing wood and installing a solar photovoltaic system were straight-forward choices as well but required analyzing how much of it the budget would allow and balancing their costs against the costs of the other products.
- Products that required analysis of durability, aesthetics, immediate and long term environmental qualities such as off-gassing and carbon footprint, and incremental cost differences.

While the first category did not require much discussion, the second and third categories required multi-faceted value engineering. Sustainable Design Consultant Andrea Traber helped the team prioritize the options and evaluate which products would provide a larger positive impact on the environment and people, and green value in terms of financial and environmental investment. In the end, the team was able to maximize the green footprint without compromising the quality and cost of the project. Value engineering examples for each category will be discussed in upcoming articles.
Be the first to comment