Earlier this year, I attended the Symposium on Taiwan-France Cooperation in Intelligent Green Buildings hosted by the National Taiwan University of Science and Technology (NTUST) and the French Office in Taipei. Taiwan and France have been actively exchanging science and technology information for more than thirty years. Sharing insights on intelligent green buildings and measurement tools is another avenue for collaboration. The session topics ranged from eco-cities to smart energy management systems to current green projects by Taiwanese and French architects in Taiwan and beyond.
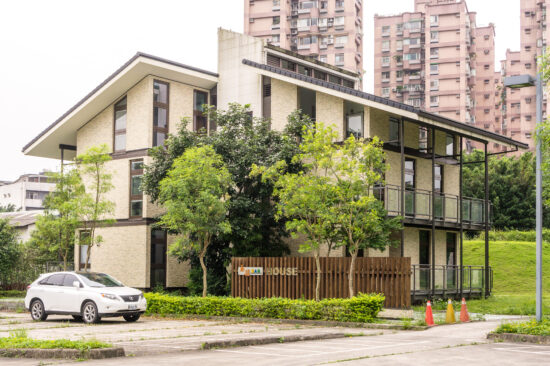
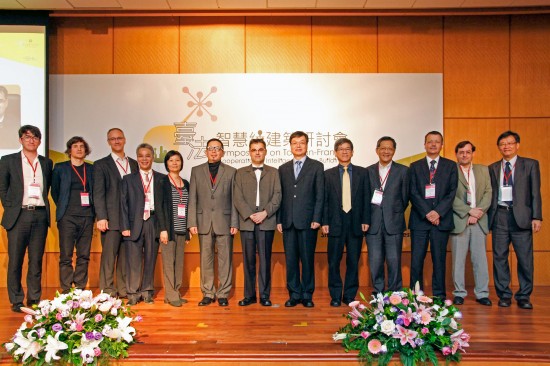
As part of the Symposium, Professor Min-Yuan Cheng, PhD from NTUST presented on and gave a tour of the MEGA House, an experimental project that explores the application of RFID (radio-frequency identification) technology throughout a building’s life-cycle starting from planning, to fabrication and post-occupancy. The project was a joint effort of the Ecological and Hazard Mitigation Engineering Research Center of NTUST and the Architecture and Building Research Institute of Taiwan’s Ministry of the Interior. Professor Cheng was the project leader in the planning, coordination, and execution of the project.
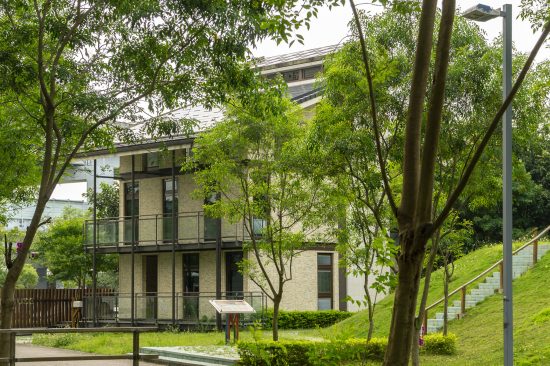
The 3-story building is an intelligent green building that utilizes green building materials (M), electronics (E), green technologies (G), and automation (A), hence the name, MEGA House (also known as the EAG House). It comprises of a concrete foundation, metal stud framing, and a prefabricated modular exterior wall panel system which can be easily assembled and disassembled for future re-use or recycling. The structure was built within three days while the entire building was completed within three months.
A key feature integral to the conception and construction process of the MEGA House is the embedment of RFID tags into various building components. RFID tags were embedded in the prefabricated exterior wall panels, exterior doors, and plumbing pipes. Each type of tag embedment has its own monitoring purpose.
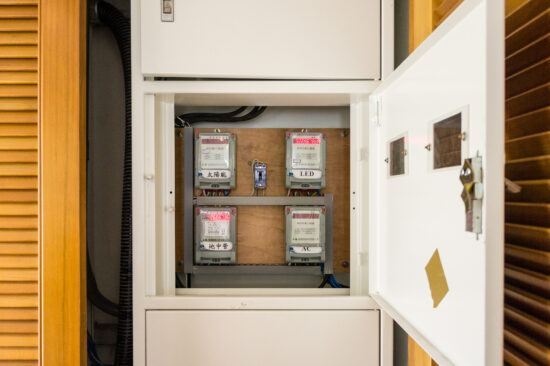
RFID-tagged exterior wall panels played an important role in enabling a controlled assembly process that was monitored in real-time. A 1/10th scaled model was first built with wall panels embedded with RFID tags during the planning phase. A specially developed real-time construction monitoring system was used to track the model assembly process through those RFID tags. The simulation derived from constructing the model then served as a template for the actual construction of the building. All full scale exterior wall panels were then tagged with RFIDs. During their transportation and storage, each panel was tracked through its RFID tag. During the construction process, each wall panel was installed in sequence per the simulation and each RFID tag transferred real time information to the engineer and/or superintendent monitoring the construction.
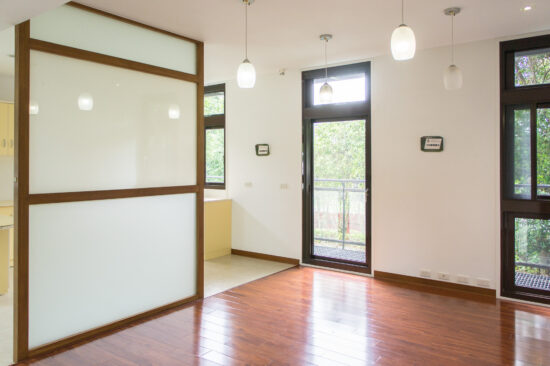
RFID-tagged doors were combined with other design strategies to help maintain the comfort level of the building. All exterior doors are tagged so that the number of occupants in the building can be tracked through the door traffic and in turn inform the heating, ventilation, and air conditioning (HVAC) system to adjust accordingly. Environmental sensors are installed at all windows and serve the same purpose of automatically managing the HVAC system. Each sensor senses radiation, outdoor temperature, relative humidity, and wind speed, and feeds the information to the main HVAC control panel. In the future, additional sensors can be installed so that the windows can automatically open and close according to the building interior conditions.
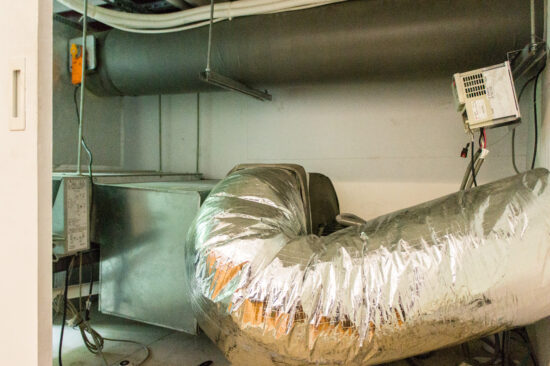
Passive design strategies such as an earth tube (also known as an earth to air heat exchanger) and a solar chimney also contribute to the MEGA House’s comfort level. An earth tube installed 13 feet (4 m) below surface outside the building foundation provides geothermal cool air in the summer and warm air in the winter from the ground and into the building. A mechanical fan helps draw in the air and a nano-air filter at the entry point of the earth tube filters the air. A solar chimney is installed over a centrally located, open style staircase so that the building’s hot air, which naturally rises, can be expelled from the solar chimney through its air vents, and if necessary, with the help of exhaust fans. This building element is extremely useful given that Taiwan’s hot weather typically starts in mid-May and lasts through mid-October.

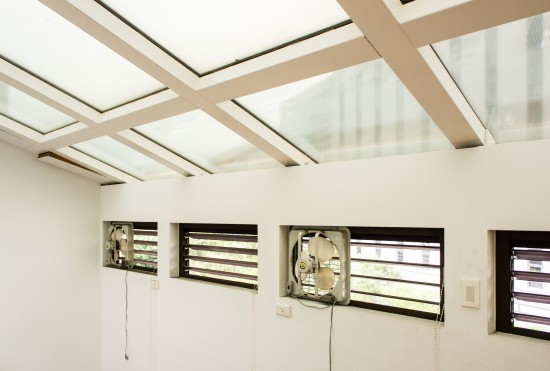
In terms of long-term maintenance of the building, RFID-tagged plumbing pipes and other design strategies were implemented to aid and minimize maintenance requirements. All plumbing pipes are tagged so that during future remodeling or deconstruction, workers can locate them in the walls and prevent potential pipe damage. The exterior wall panels and the 3-in-1 solar PV energy glass roofing are all coated with nano-coating so that it reduces the need for frequent cleaning. Fewer scheduled cleanings means reduced maintenance and operation costs.
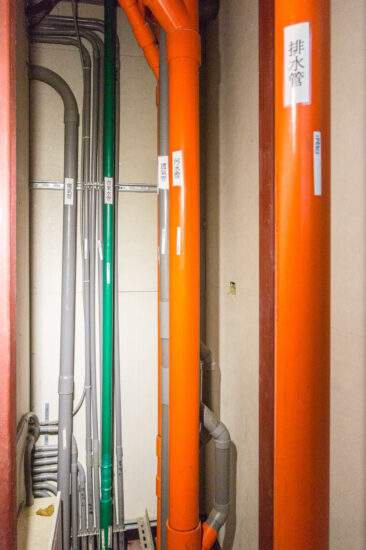
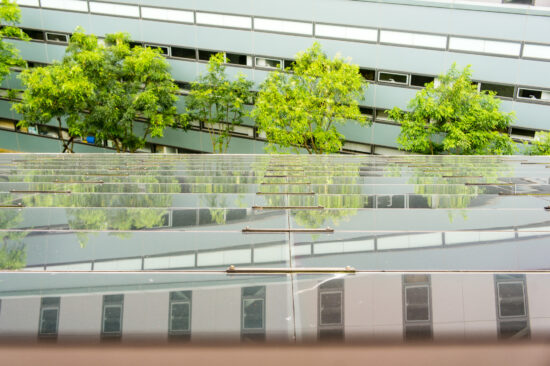
Post-construction, the project team collected experimental data from the automation and monitoring system over time and continues to promote its research resulting from the MEGA House. For the near future, it is also considering having people live full-time in this experimental building to re-confirm the livability and the continued effectiveness of the various automation and monitoring systems.
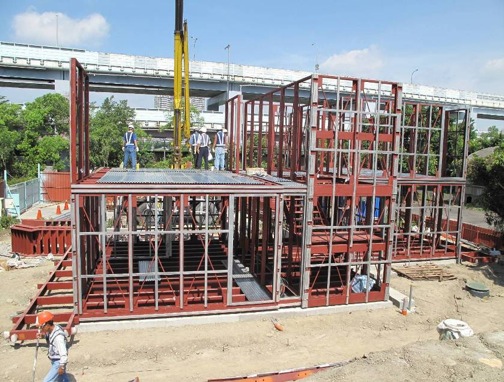
The network of RFID tags, sensors, and metering panels enables the MEGA House to be an “intelligent” building—intelligent in its conception, intelligent in its construction process, and intelligent in its post-occupancy phase. Coordinated with other green building measures, the network allows the HVAC systems to automatically maintain the indoor environment at its optimal efficiency based on occupant requirements.
The inclusion of RFID tags can help optimize construction techniques and processes including prefabrication and installation, support the construction schedule, and minimize potential mistakes. Their integration with monitoring sensors and automated responsive systems in intelligent buildings will allow owners to maintain their property in a smart, safe, and green manner.
Be the first to comment