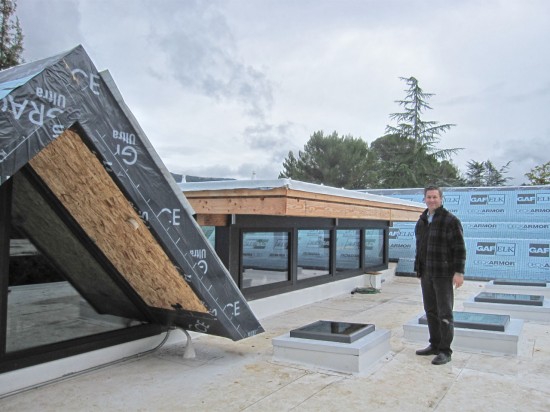
My first in-depth encounter with Eichler homes was a few years ago on a blazing hot 90°F Saturday afternoon in Palo Alto, California. I participated in a self-guided Eichler Home Tour which benefited Habitat for Humanity. It was such a treat to get a glimpse into what lay within the Eichler homes that modernized the California landscape of 1950s-1970s residential subdivision, tract housing developments.
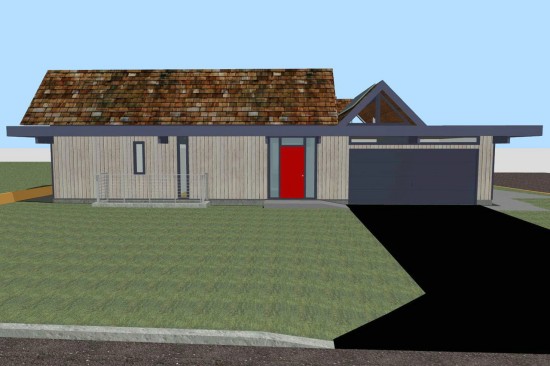
Recently, I had the opportunity to visit an Eichler home that is currently undergoing creative modernization way beyond the typical interior renovations carried out in most Eichler homes. The Green Eichler Remodel not only respects the existing building envelope, footprint, and floor plan, but also uses smart, green building strategies to optimize the original design concepts and double the floor space by going downwards!
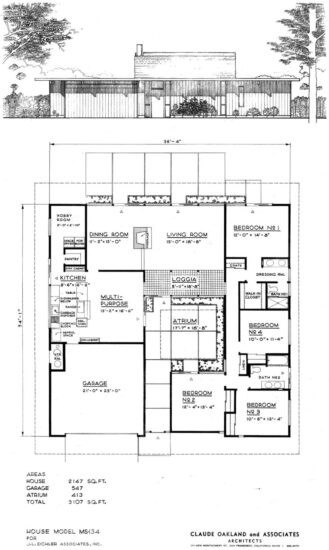
The Green Eichler Remodel occupies a corner lot in a small scaled Eichler development in Monte Sereno, California. The original 1969 Eichler building was designed by architect Claude Oakland. 42 years later, it is being transformed into a sustainable model of the 21st century. Owner Bryan Mekechuk is the mastermind of this sophisticated and well thought out remodel project. He acts as his own client as well as builder (Teamwrkx Construction), not only extensively researching building systems and components, but also picking up materials and supervising quality control on the jobsite.
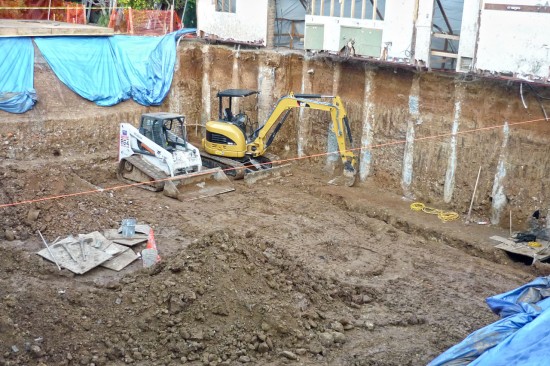
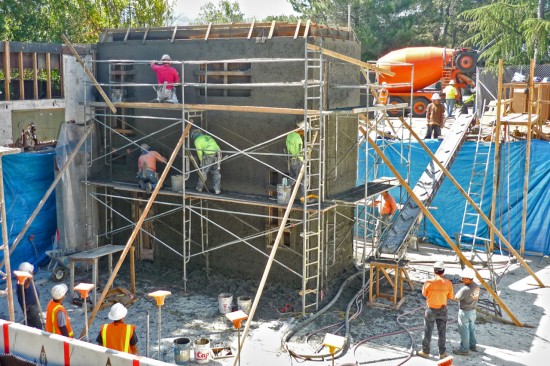
The Mekechuk family’s growing spatial needs prompted Bryan to find a way to continue living in their much loved Eichler home. Without committing the blasphemy of building upward, Bryan decided to double the square footage by building below ground. He pledged to remodel and expand the house with green design and construction strategies which would allow him to minimize environmental impacts throughout the construction process as well as post-occupancy. Those strategies would also translate into comfortable living spaces, minimal maintenance, and low utility costs.
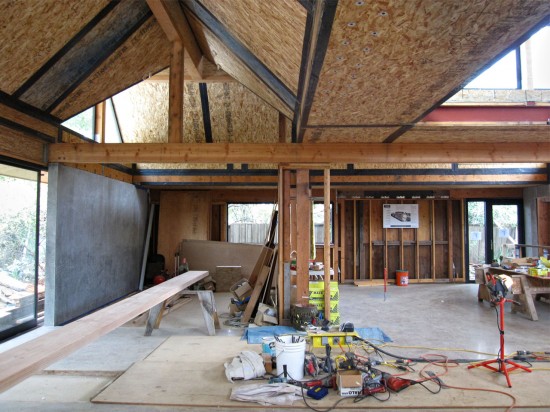
The design of the remodel has been shaped by multiple factors:
- The family’s desire to enhance the existing architectural characteristics of their Eichler home: the open style floor plan, the transparency between indoor and outdoor spaces, and exposed structure.
- Bryan’s fondness for the works of architect Pierre Koenig who is noted for his Case Study Houses and steel and glass construction.
- Bryan’s requirement to cohesively integrate all the green building energy efficiency components into the overall design of the architectural, structural, mechanical, and electrical systems.
The project will be targeting a LEED for Homes Platinum level certification as well as 0.6 air change certification per Passive House standards.
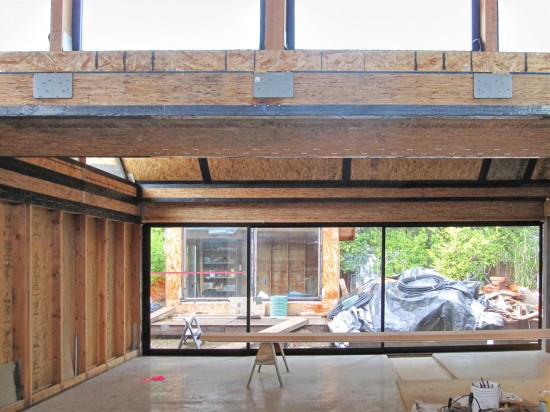
The Green Eichler Remodel exceeds Title 24, Part 6 (California’s Energy Efficiency Standards for
Residential and Nonresidential Buildings) requirements by 72.9%. This extremely energy efficient and air tight building achieves this by using a combination of smart, but basic, active and passive solar design principles. The project’s active solar component, a 10.32 kW solar photovoltaic system consisting of 48 panels at 215 watts per panel, will produce more than 100% of the family’s electrical needs which include two electrical vehicles charging stations. The family’s new electric car, the Nissan Leaf, is currently on order.
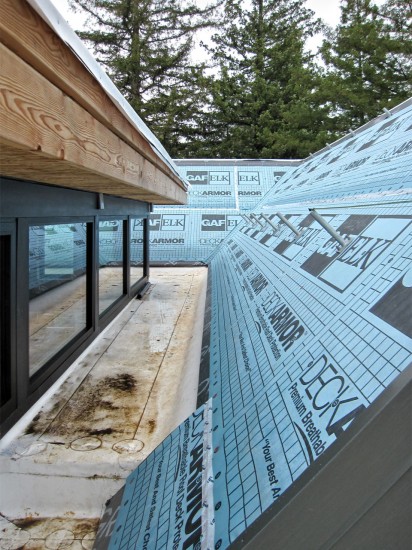
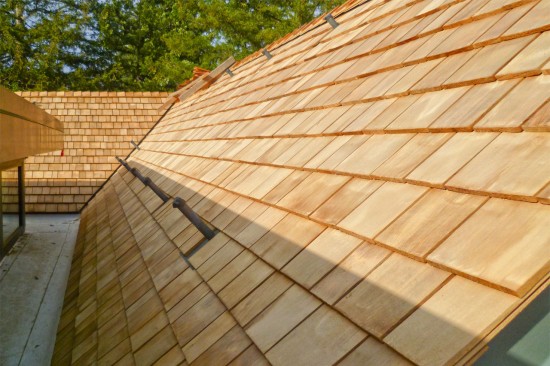
The house’s passive solar components help to keep the heat out on hot days and to provide extra insulation on cold days, consequently minimizing annual mechanical cooling and heating loads. The components include:
- minimal and shaded glazing on the south side;
- a flat “cool roof” covered with a 60 mil TPO membrane;
- roofs constructed with Insulspan SIPs (Structural Insulating Panel System) and built by Earth Bound Homes; and
- large windows on the north side and clerestory windows in the center of the house to provide natural light throughout the house.
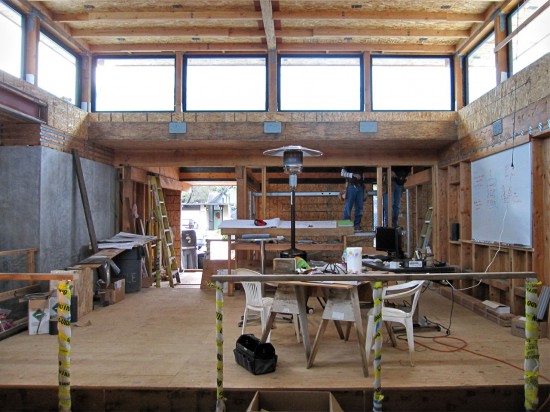
My favorite passive solar design element is the transformed atrium which resulted from the addition of the basement. The decision to add living spaces in a basement was shaped by Bryan’s experiences of spending a good part of his life “living in basements” like many other fellow Canadians. The biggest concern was how to create comfortable subterranean spaces with enough natural light throughout the day. Light-wells and windows were located along the exterior walls to provide daylight into the bedrooms. However, it was the solution of providing light into the basement’s main space that turned out to be an exercise in ingenuity. The existing atrium was transformed into a passive solar design mechanism which maximizes the benefits it receives from the sun. A roof was added to it, its four walls were raised to accommodate clerestory windows, and its floor was opened up and replaced by two sets of bridges overlooking the lower level. The resulting two storey atrium brings natural light to the main and lower levels, making the rooms comfortable and minimizing the need for electrical lighting throughout the day. At the same time, the exterior overhangs each with their own calculated depth help minimize solar heat gain in the summer.
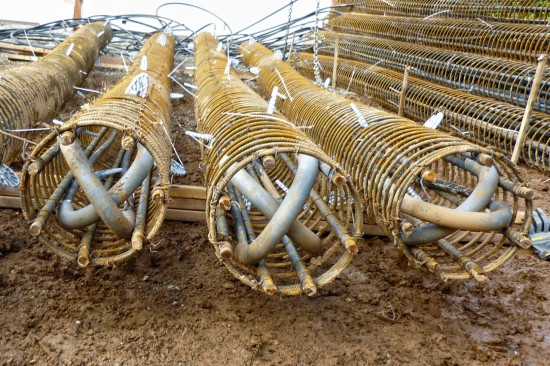
Another important design component that allows the family to reduce dependency on electricity is the geothermal/ground source heat pump (GSHP). Tapping into the Earth’s natural heat, the heat exchanger provides hot water for the domestic hot water and radiant floor heating systems, and cold water for air conditioning. Its waste hot water will be directed to the swimming pool while the waste cold water will be pumped to the wine cellar’s cooling system. Recycle and re-use at its best.
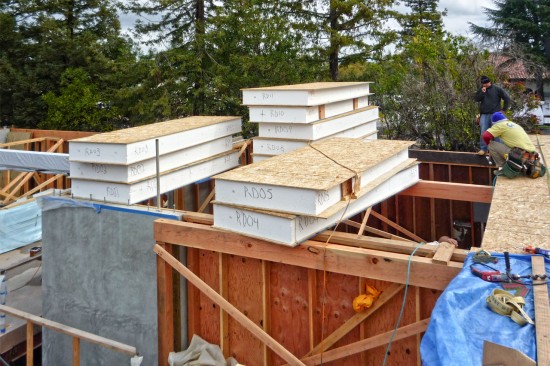

As a counterpart to green design strategies, green construction strategies were implemented to minimize construction waste. Prefabricated building components such as SIPs were used for the roof and hollow core concrete panels were used for the floor. Because they are manufactured in controlled environments, material usage and assembly are precise which then get translated into minimized waste and construction time. Responsibly harvested, FSC certified selected structural studs were used for framing because their superior quality had less room for waste than did standard grade 1 or better studs. Instead of using long span engineered beams, Bryan used reclaimed wood, including a 40 ft long Idaho pine, to showcase in the living room ceiling space.
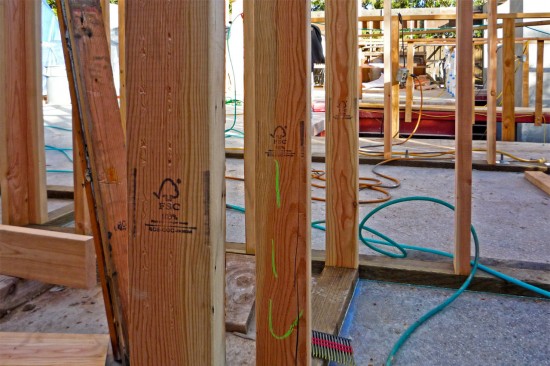
The architecture of the Green Eichler Remodel is elegant, but there is more to it than meets the eye. It has been intimately defined by structural, mechanical, and green strategy needs. This project goes beyond fulfilling a checklist of green points. It represents a client/builder’s true understanding of the importance of well integrated and self-sustaining design. Per Bryan Mekechuk:
“First, the design must be integrated across disciplines (e.g., architectural, structural and HVAC), and then it has to be built using sustainable materials in a sustainable manner. This project would not have been possible without a complete, integrated team. We have been fortunate to be able to work with a large group of extremely talented professionals who have world-class design expertise completed by world-class construction expertise. Our broad and deep team was critical in making our project happen.”

I have been impressed by Bryan’s knowledge of every nut, bolt, pipe, and piece of wood that has gone into his house. I look forward to my next visit of the project to report back on the finished product including the interior finishes. In the meantime, please check out his blog that tracks the construction progress since day 1.
u go u
nice